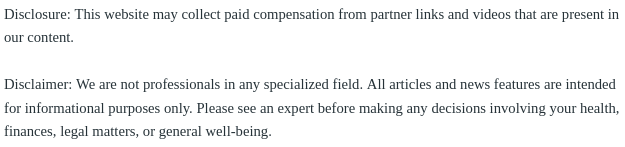
In the world of business operations, maintaining the infrastructure and essential systems is a crucial task that ensures efficiency and longevity. Industry professionals have a perennial debate about the best maintenance strategy to employ. Two main strategies dominate this discussion: preventive maintenance and corrective maintenance. Both strategies aim to optimize performance and reduce downtime of equipment and facilities, but they do so in different ways.
Understanding the difference between these two approaches is vital for any business, from an AC company ensuring optimal climate control to septic tank pumpers maintaining sanitation systems or even asphalt companies providing safe road surfaces. In this article, we delve into the differences between these approaches, explore their significant impacts, discuss budgeting strategies, and examine the role of technology and training in maintenance. Furthermore, we’ll provide insights into how organizations can overcome challenges associated with maintenance planning and how outsourcing and automation can refocus their strategic maintenance efforts. Whether your business is involved in masonry service, lawn fertilizing, or even fence installation services, a well-planned maintenance strategy is essential for sustained growth and operational efficiency.
What is the difference between preventative and corrective maintenance?
Preventive maintenance refers to the systematic approach of regularly inspecting and servicing assets to prevent breakdowns and malfunctions. This form of maintenance is planned and scheduled based on time or usage and helps keep systems running smoothly with minimal unexpected downtimes. Corrective maintenance, on the other hand, is a reactive approach where repairs are made after the equipment has failed or issues have arisen.
Asphalt companies often rely on preventive maintenance to ensure that roads and pavements remain in top condition, extending their lifespan and enhancing safety for users. In contrast, corrective maintenance can be more costly and disruptive as it involves repairing damage after it occurs. The key distinction is that preventive maintenance is proactive, aiming to mitigate issues before they arise, while corrective maintenance addresses problems after they have already impacted the system.
Preventive maintenance helps businesses avoid unexpected failures and costly repairs that result from a purely corrective maintenance approach. By scheduling regular checkups and maintenance tasks, businesses like masonry service providers can enhance the durability and reliability of their tools and equipment. The objective is not only to maintain functionality but also to optimize performance and predict potential failures before they occur rather than dealing with them post-factum.
Why is preventative maintenance important for businesses?
Preventive maintenance is crucial for businesses because it significantly reduces the risk of unexpected equipment failures, which can lead to costly repairs and operational downtimes. For a masonry service, consistent preventive maintenance can ensure that the heavy-duty equipment remains in good condition, allowing projects to be completed on time and within budget. Regularly serviced equipment also tends to have a longer lifespan, which presents a better return on investment over the years.
Businesses such as those that offer septic tank pumping services benefit greatly from a preventive maintenance approach. By proactively addressing potential blockages or system failures, they can prevent environmental hazards and service interruptions, which could otherwise lead to fines and loss of client trust. Thus, preventive maintenance supports business continuity and enhances customer satisfaction through the avoidance of unwanted service interruptions.
Furthermore, preventive maintenance allows businesses to budget their maintenance expenses more predictively. For example, an AC company can incorporate regular system inspections into their operational routine, minimizing the need for sudden expenditure on emergency repairs. The ripple effect of this approach is improved financial planning, enhanced system reliability, and increased customer loyalty, as services are delivered smoothly and efficiently.
How can corrective maintenance impact your budget?
Corrective maintenance, unlike preventive maintenance, can have significant implications on a company’s budget due to its reactive nature. An AC company may face unexpected financial stress by suddenly having to repair or replace malfunctioning units during peak operational times. These unplanned repairs tend to be more expensive due to the urgent nature and potential for more extensive damage if regular maintenance is not performed.
Corrective maintenance not only requires unexpected funds for repairs but can also result in lost revenue due to operational downtimes. Septic tank pumpers, for instance, need to avoid any service halts during busy seasons. Unscheduled disruptions can also damage professional reputations and lead to customer dissatisfaction, potentially losing long-term clientele to competitors who maintain consistency in their service delivery.
While certain industries may occasionally rely on corrective maintenance, integrating more preventive practices could alleviate some financial strain. Businesses like local locksmith services will find that the cost of emergency repairs due to neglect can outweigh the investment in regular maintenance. Implementing a balanced maintenance strategy helps stabilize the maintenance budget and reduce potential financial risks.
What are key strategies for budgeting preventive maintenance?
Budgeting for preventive maintenance involves strategic planning to ensure that funds are allocated appropriately to cover routine maintenance activities. One effective strategy is to conduct a thorough assessment of all equipment and infrastructure, identifying which assets require more frequent attention. This process helps prioritize spending and ensure that the most critical components receive the necessary care.
For businesses involved in dumpster rental, creating a maintenance calendar can aid in the budgeting process. By mapping out inspections and service tasks over a fiscal year, companies can allocate resources more efficiently, avoiding the financial shock of unplanned corrective maintenance. This scheduled approach also allows for flexibility in adjusting plans based on the evolving needs and usage patterns of the machinery or equipment.
A proactive approach to maintenance also involves investing in training and development for staff to handle routine checks and minor repairs internally. For example, a local locksmith business could benefit from team members being cross-trained to handle basic maintenance tasks, reducing external service costs. By incorporating preventive maintenance into the organizational culture, businesses can more effectively manage costs and enhance operational efficiency.
How do you prioritize maintenance tasks?
Prioritizing maintenance tasks requires a systematic approach where tasks are ranked based on their importance and potential impact on business operations. Septic tank pumpers, for instance, may need to address maintenance issues based on urgency, considering the consequences of potential system failures and regulatory compliance requirements. Task prioritization ensures that critical systems receive the attention they need to function optimally.
A well-structured priority system typically involves an assessment of the risk associated with each piece of equipment or infrastructure. In the case of fence installation services, this might involve analyzing weather-related wear and potential security implications of neglected repairs. By using a risk-based approach, businesses can focus their maintenance efforts on areas that serve to mitigate the highest risks.
To effectively prioritize tasks, it is beneficial for businesses to adopt a collaborative approach involving multiple stakeholders such as operational managers and maintenance personnel. This ensures a comprehensive understanding of operational needs and maintenance requirements, paving the way for informed decision-making. By involving diverse perspectives, organizations can better allocate resources, time, and personnel to maintain critical operations efficiently.
What roles do technology and automation play?
The advent of technology and automation has transformed the landscape of maintenance management by offering smarter, more efficient ways to handle preventive and corrective maintenance. For industries like lawn fertilizing businesses, technology offers new tools such as automated scheduling and predictive analytics that enhance the ability to plan and react promptly. This technological integration results in increased efficiency and cost savings over the long term.
Automation tools provide companies with the capability to handle routine maintenance tasks without constant human oversight. Businesses such as a local locksmith service can use automated systems to flag when equipment needs attention, thereby ensuring timely maintenance and preventing costly corrective actions. This leads to prolonged equipment life and minimizes interruptions in services provided to customers.
Technology also aids in data collection and analysis, providing businesses with actionable insights into their maintenance operations. These insights allow companies to fine-tune their preventive maintenance strategies, ultimately reducing operational costs and enhancing service reliability. Additionally, businesses can leverage these technological tools to measure maintenance effectiveness, supporting continuous improvement initiatives across the board.
How do you measure the effectiveness of your maintenance strategy?
Measuring the effectiveness of a maintenance strategy involves evaluating various metrics that reflect the performance and efficiency of maintenance activities. For a faux stone company, key performance indicators (KPIs) such as equipment uptime, maintenance cost per unit, and mean time between failures provide insights into the effectiveness of existing maintenance plans. Tracking these metrics helps identify areas for improvement and ensures that maintenance investments are yielding anticipated returns.
Another approach involves assessing the frequency and severity of unplanned corrective maintenance incidents. High occurrences of unexpected repairs might indicate limitations in the preventive maintenance strategy that need addressing. By regularly reviewing these incidents, businesses can refine their maintenance schedules to better align with operational needs and reduce unexpected hurdles.
Feedback from maintenance teams and other stakeholders is also essential in measuring strategy effectiveness. Practical insights from those directly involved in maintenance tasks can highlight gaps in current practices and point toward potential enhancements. Establishing open communication channels allows businesses to adapt strategies dynamically and sustain the reliability of their maintenance processes over time.
What are the challenges of implementing maintenance plans?
Implementing maintenance plans comes with an array of challenges, and understanding these obstacles is key to overcoming them effectively. One common issue is resistance to change, especially when transitioning from corrective maintenance to a more preventive approach. Employees accustomed to reactive maintenance may find adjustment to scheduled, proactive methods challenging, which can hinder the adoption of new processes.
Fence installation services, for instance, may face logistical challenges when integrating preventive maintenance into their operational workflow. Coordinating maintenance schedules with ongoing projects requires effective communication and planning to ensure minimal disruption to business operations. Finding the balance between ensuring equipment readiness and enhancing productivity is a delicate process that businesses must navigate carefully.
Another obstacle is the initial cost associated with implementing preventive maintenance measures. While long-term savings are significant, the upfront investment in training, technology, and systems might dissuade some businesses. It is important to present a clear return on investment argument to stakeholders, emphasizing the positive impact on operational efficiency and service reliability that preventive maintenance ultimately offers.
How can staff training enhance maintenance outcomes?
Proper staff training is crucial for enhancing maintenance outcomes, as it ensures that all personnel are equipped with the necessary skills and knowledge to effectively perform their duties. In the HVAC Service industry, for example, trained technicians can perform routine inspections and minor repairs in-house, reducing reliance on external service providers and cutting down maintenance costs.
Training programs should focus on both the technical aspects and the importance of a proactive maintenance culture in the organization. Well-informed staff will more likely identify and report potential issues before they develop into significant problems, aligning with the goals of a preventive maintenance strategy. This proactive culture promotes a more attentive workforce that prioritizes the integrity and reliability of business operations.
Additionally, continuous training helps staff remain informed about the latest technological advancements and industry best practices. Businesses like those managing lawn fertilizing operations can benefit from training on the latest tools and software to optimize maintenance scheduling and execution. By investing in their workforce, companies enhance maintenance outcomes and reinforce a culture that values efficiency and high-quality service delivery.
What role does outsourcing play in maintenance management?
Outsourcing maintenance tasks can provide businesses with access to specialized expertise and resources, enhancing their capacity to perform both preventive and corrective maintenance effectively. For lawn fertilizing businesses, outsourcing can mean leveraging the knowledge and experience of third-party professionals to ensure optimal equipment functionality and adherence to industry standards.
Outsourcing enables companies to focus on their core operations while leaving specialized maintenance tasks to experts. For instance, fence installation services may choose to outsource specific maintenance tasks that require niche skills or equipment that the company does not possess in-house. This approach can increase operational efficiency and ensure that all equipment and facilities are maintained to the highest standards.
However, when outsourcing, it is essential to establish clear communication and performance expectations with service providers. Ensuring alignment with preventive maintenance objectives is crucial, as it impacts the overall strategic direction of maintenance management. Properly managed, outsourcing can provide significant value by enhancing maintenance efficiency and allowing businesses to adapt more flexibly to fluctuating demands.
Developing an effective maintenance strategy requires a nuanced understanding of both preventive and corrective maintenance approaches. Each approach holds its unique advantages and challenges, and businesses must identify the balance that best suits their operational needs and industry demands. With the integration of technology, strategic budgeting, and investment in staff training, businesses can significantly enhance the reliability and efficiency of their maintenance operations.
Key to successful maintenance management is adopting a proactive mindset that values preventive measures, supported by periodic reviews and adjustments to maintenance plans. While corrective maintenance will always have a place in the strategic toolkit, its reliance can be minimized through deliberate efforts to maintain equipment proactively. This balance leads to increased service reliability, enhanced safety, and more predictable financial planning.
For businesses across diverse industries, from asphalt companies to faux stone companies, the importance of a robust, integrated maintenance strategy cannot be overstated. Equipped with insights from this article, organizations are better positioned to implement effective maintenance management practices, ultimately contributing to their long-term success and sustainability. By continually optimizing these strategies, businesses can ensure consistent service delivery and enhance overall operational efficiency.